Pump Stator Guideline-For Progressive Cavity Pumps
The stator is one of the key pump parts of a progressive cavity pump. People also called it PC(Progressive Cavity) pump bushing. The PC pump stators usually consist of an external shell and an internal lining.To get more news about
screw pump stator, you can visit hw-screwpump.com official website.
For the screw pump stator shell, the raw materials are normally inelastic and hard. Such as metals, plastics or even ceramics. Generally, the frequently used types are steel with painting or stainless steel. This rule applies to most progressive cavity pump brands like NETZSCH, MONO, SEEPEX, ALLWEILER, etc.
However, the lining materials are usually rubber-like elastic. And many types below of raw materials could be your choice. You can select the correct one based on your PC pump applications. In some special cases, it can also be made of plastic, teflon or metal.Before we decide on the raw material for the single screw pump stator, we must consider the pump working conditions and the mediums which go through the PC pump. That means we should know the material’s corrosion resistance, wear resistance, swelling resistance, and working temperature.
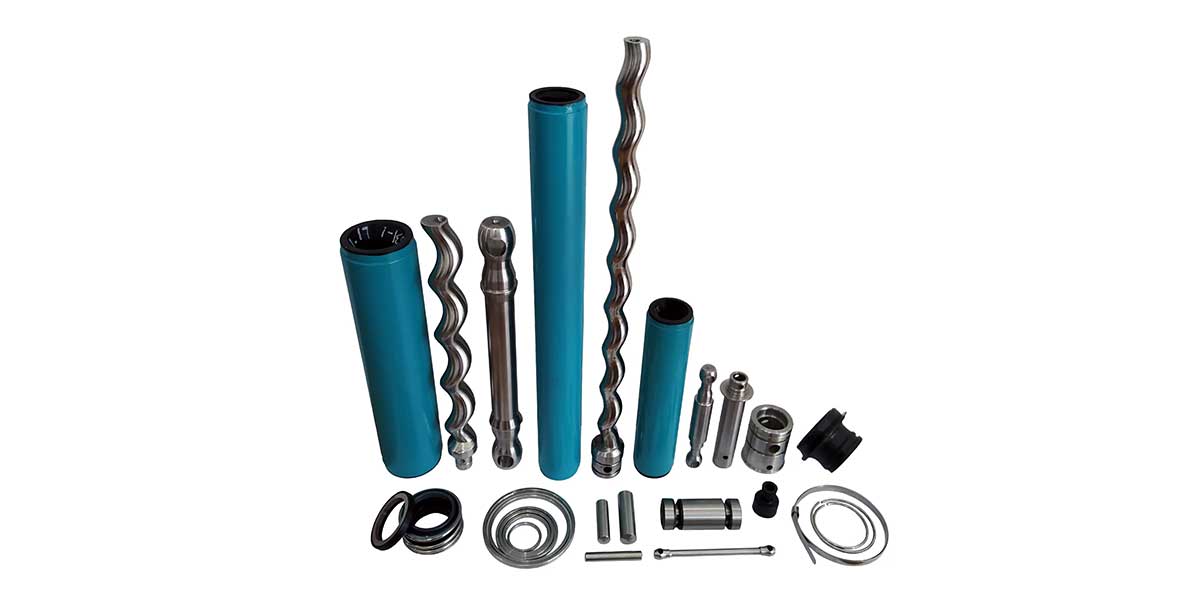
When the temperature of the transported fluid is between 0 and 60°C, all lining materials mentioned above can work; For low-temperature applications (below 0°C) or light acids and bases, EPDM will generally be a good choice. However, EPDM stator is not allowed in the conditions of mineral oils.
For the pumps to work in chemical conditions, it is a little complex. So we must decide on the lining materials case by case. Please be aware that Nitrile is a suggested stator material when the progressive cavity pumps work in non-aggressive conditions like water treatment, biogas, food content, etc. Nitrile is popular and widely used as it covers 80% of the pump stator lining in the market.
When your pump works for aggressive chemical applications or at high temperatures, the Viton would be an option in most cases. But please note that Viton has its limits. It has low resistance to water vapor and caustic soda (NaOH).
If you mainly need to consider the abrasion resistance of the stator but think Viton is a little poor in a way, NBR is usually a good compromise. And for some extreme cases, Buna CD is recommended.
For food application pumps, NBR, EPDM or some Viton? would be a good choice. They are usually white or black. The “Lining Material Features of Progressive Cavity Pumps” is below for your better understanding.Generally, the quality of the stator lining will directly affect the service life of a pump stator. In normal conditions, the pump stator needs to replace every 1 to 2 years under normal pumping conditions.
When we don’t select the rubber sleeve (internal lining) properly, the rubber sleeve may be easier to wear out, corrode or quickly age. In severe cases, the lining may partly damage or completely fall off the steel shell. So we need to understand the basic features of the optional stator materials and their adaptability to various mediums.Based on the working principle of progressing cavity pump, we know the pump stators and rotors are interference fit with each other. Though the rubber-like lining is elastic, there is natural wear. In addition, progressive cavity pumps usually work in viscous fluid and mediums containing solid particles. So natural wear is normal and unavoidable.
Another type of wear is unnatural. Maybe it’s caused by degumming or improper operation. When there are some hard particles go into the working cavity, it increases the unnatural wear. In case an improper operation happens, the PC pump may be reversed or unloaded which would cause dry operation or even burnt out.
When there is a problem with the surface treatment in the stator inner hole, there pump stator quality would be not good. And if the adhesive used in the stator manufacturing is invalid or the vulcanization process is not good enough, the rubber lining would fall off and be tored in working.